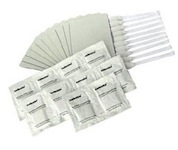
Does your ID Card Printer Ribbons Keep Breaking?
Here are some of the most common reasons why ribbons can break and how to avoid them:
1. You have never cleaned your card printer. Card printers are very sensitive to dust and other airborne debris. Tiny particles of dust and oil from fingerprints cause all kinds of problems. Cleaning your printer after every ribbon change is a good rule of thumb. And if your printer has not been used in a while, I’d highly recommend cleaning it before you start printing again.
2. You are trying to print over the edge of the card. Standard direct-to-card printers print directly to the card surface, and can get pretty close to the edge (edge-to-edge) but cannot print a full bleed (over-the-edge) like retransfer printers can. Trying to achieve this may result in the ribbon breaking. Every printer is different, but you should make a point to check the printer’s top of form settings and print an alignment test card to see where the print is actually going on the card.
3. You have increased the color intensity. If the heat settings are too hot, ribbons are likely to tear. Your printer’s color intensity can be adjusted according to what printer model you have. For example, adjustments for Magicard printers can be made by going to the “Printing Preferences” settings and then to “Color Correction” where you can set it to “Gamma One” or “Gamma Two.” With Fargo printers, you can go to the Tool Box and under “Advanced Settings,” adjust the color intensity. For most other printers, you can simply go to the “Printing Preferences” settings within the ID card software to adjust the color settings. If the color is too dark, the printhead is getting too hot which ultimately breaks the ribbon.
It’s important to note that the most effective way to adjust your color intensity is to call our in-house Technical Support Team at (866) 433-9737 to assist you.
And as with any other printer questions you may have, our in-house Technical Support Team is an invaluable resource for you. From one of their tailored training sessions to printer support, you can count on this experienced and exceptionally knowledgeable team to help.
4. Your printer is old and you have never re-calibrated the sensors. All equipment is subject to wear and tear. Even if your card count is low, basic maintenance is required. Printer user guides provide easy to follow instructions for re-calibrating a ribbon sensor. It’s also a good idea to make sure you have the latest firmware and driver installed. Finally, when it’s time to replace the ribbon, calibrate the ribbon and sensor adjustments according to the manufacturer’s specifications in the user manual.
Tips: Fixing a broken printer ribbon is easy! Simply tape the ribbon back together, advance the ribbon forward, and resume card printing. While this is a simple fix, improper use can lead to a costly repair or an early printer replacement.